
The first Airbus A321XLR (MSN11000) has been structurally completed at Airbus’ Final Assembly Line (FAL) at Hamburg, Germany.
Major Component Assemblies for the aircraft were shipped from several sites including fuselage sections from Saint Nazaire in France and wings from Broughton, Wales.
The aircraft will now be fitted out with extensive test equipment as well as having its CFM Leap engines installed before commencing the certification programme for the variant.
Michael Menking, Head of the A320 Family Programme explains: “For the A321 Family, we have started all the head-of-versions in Hamburg — the real first ones — and it is our intention to build these aircraft also at the other sites.”
“We are currently on the way to also have the A321XLR delivered out of other Single Aisle FALs. So it is important for sure that all the teams learn from the experience in Hamburg so we can bring this knowledge to the other facilities. This is also what we are doing with the A320 Family Airspace cabin which we started in Hamburg.”
Airbus explains how it went through the FAL…
Once all the MCAs for the initial -XLR aircraft had reached the FAL they subsequently came together at a series of “Stations” to create a whole recognisable aircraft. The journey through these stations took approximately four weeks and comprised the following:
At Station 42/43, the open and separate aft and forward fuselage sections offered the accessibility to receive their fully equipped monuments (galleys, lavatories).
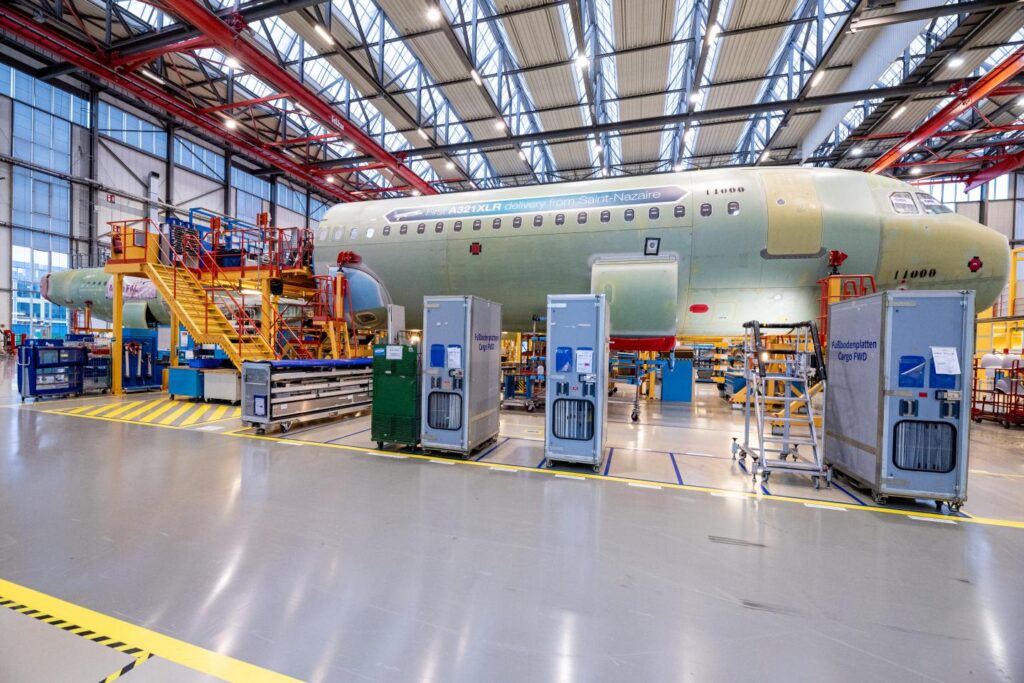
Subsequent “join-up” of these fuselage sections and final installation of the monuments took place at Station 41. Here over 3,000 rivets joined the forward and rear fuselage sections. Importantly, these fuselage sections contained the A321XLR’s vital new enabler: its special Rear-Centre-Tank (RCT) produced by Premium Aerotec. The RCT holds the extra 12,900 litres of fuel needed for its very long range 4,700nm capability. The XLR’s lower fuselage also contains a larger waste-water tank for the extra long flights. In addition, the interior furnishing (floor panels, cargo loading system and cockpit linings) and cabin electrical systems were also fitted at Station 41.
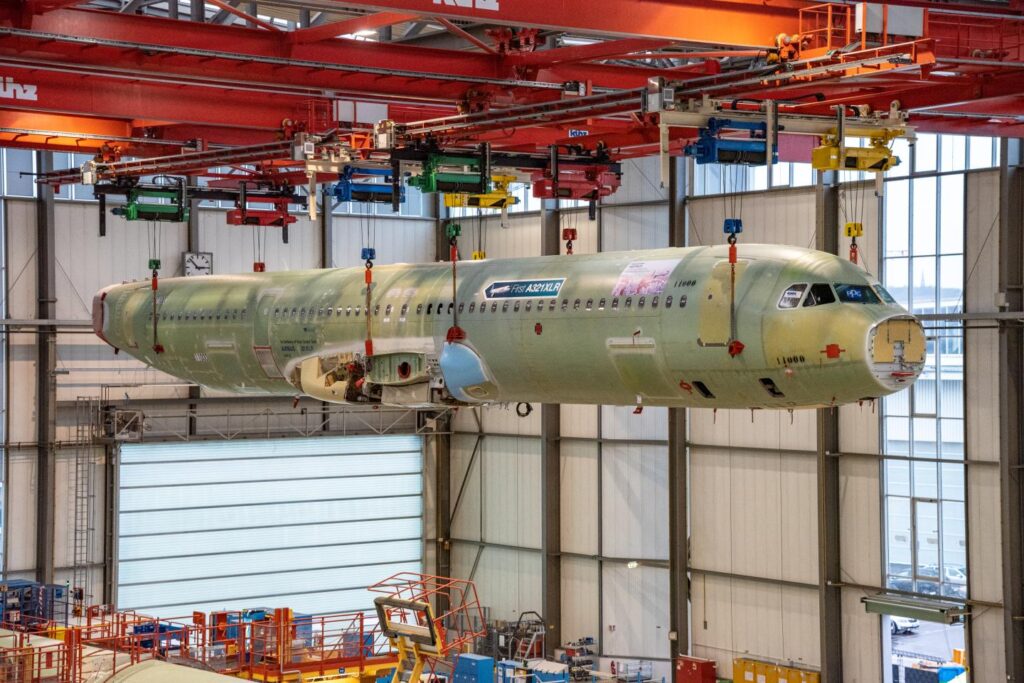
With the above stage completed, the teams in the FAL carefully raised the whole fuselage section by overhead crane and then lowered it into a jig at the next station: Station 40. This was the most visually impressive stage, where they physically positioned the awaiting wing and landing gear assemblies right up to their new fuselage with sub-millimetric precision.
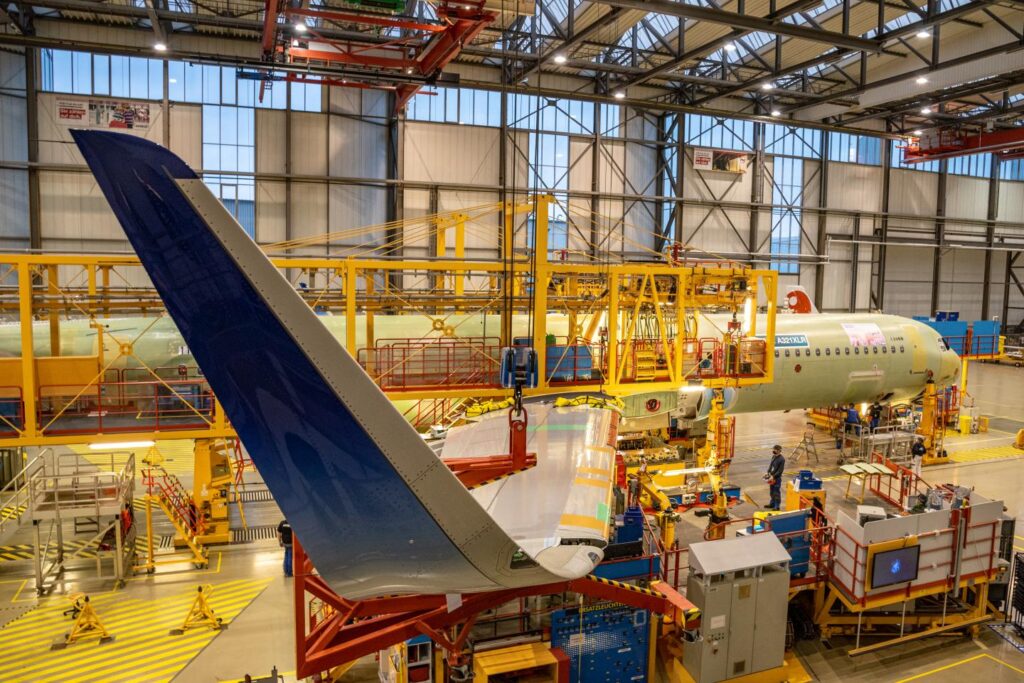
Around 2,400 rivets were then used to ensure a robust connection of both wings to the fuselage. Here the aircraft also received its Toulouse-made engine pylons. Another milestone at this station was the functional electrical “power-on”. From then on the aircraft no longer needed a crane, since it could be pulled on its own wheels to the next station.
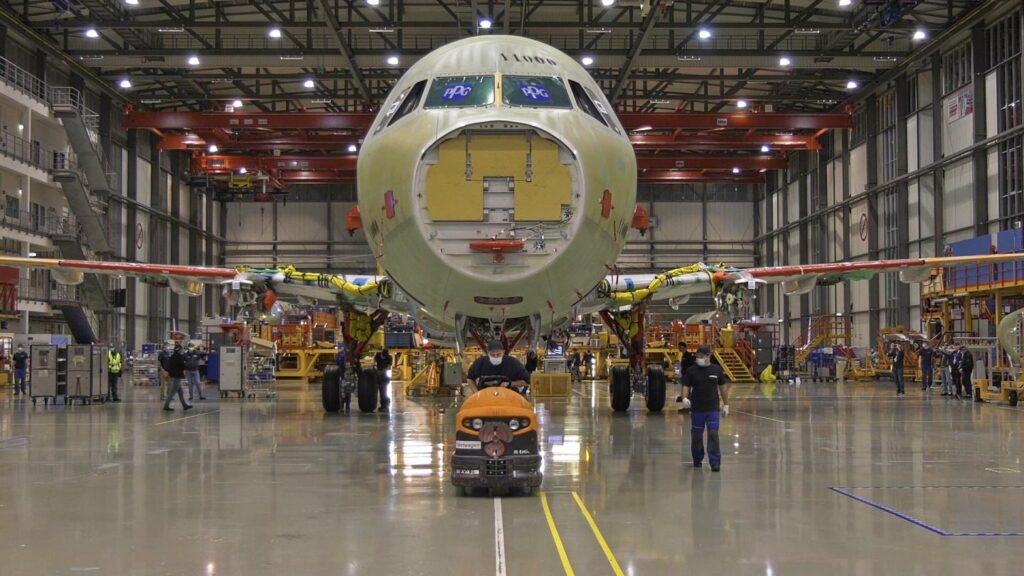
Station 35 saw the installation of the horizontal and vertical tailplanes (the HTP from Getafe in Spain, and the VTP from Stade in Germany), the tail cone, inner flaps, main landing gear doors, radome, weather radar, air ducts, air conditioning system, water system, fuel-system (which is modified for the RCT on -XLR), belly fairing, the APU, and all the passenger and cargo doors. The hydraulic system “power on” was also performed here, as well as the installation of cabin linings, hat racks, passenger service channel and cargo compartment panels. Finally the fuel tanks were sealed at Station 35.
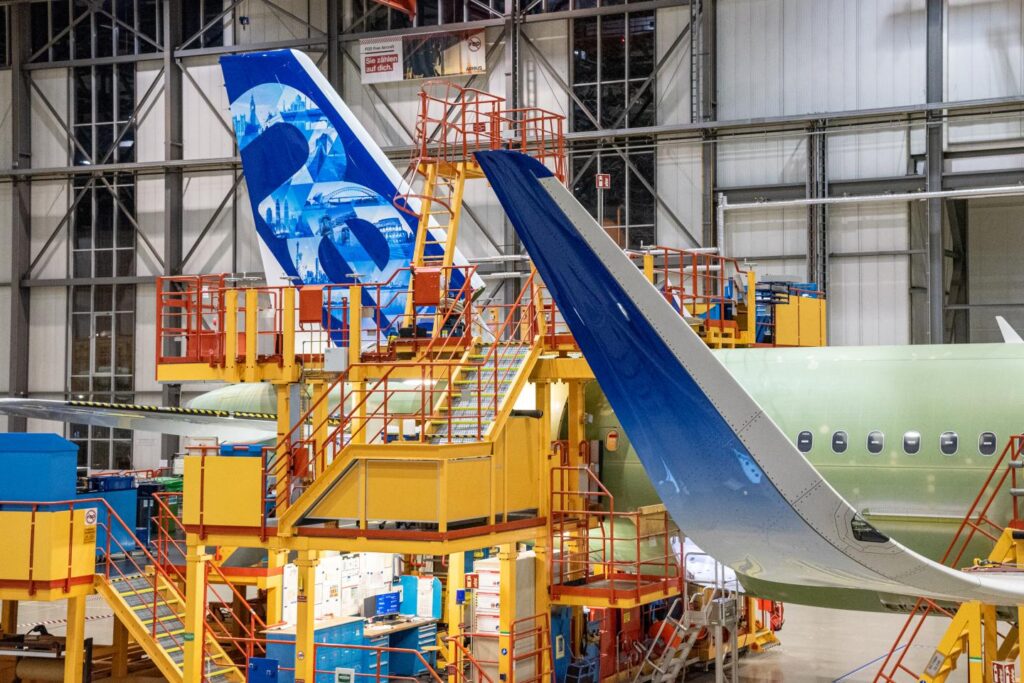
All images and text are copyright of Airbus.